The process of precision sheet metal fabrication involves designing, material selection, cutting, forming, welding, and quality control to create detailed, custom metal parts.
Material Selection
The right material selection is the cornerstone of any successful precision sheet metal fabrication. Usually, the application of a given sheet moves from stainless steel, through aluminum, to brass in terms of cost and specific properties. When parts need to be made for medical devices, where long-term durability and cleanliness are central concerns, engineers select stainless steel that provides a lasting value of being strong, corrosion-resistant, and unchanging in color. For more lightweight, malleable aluminum, this metal is often found in the aerospace sector, where its properties promote fuel efficiency and ease of assembly. Additionally, as an aesthetically pleasant metal with the properties of being in the yellow range, it is also highly suitable for decorative applications. For instance, high-end brass is selected for mixed-alloy parts of various high-end furniture goods. In short, the selection of the right material takes into account the use of the part, the environment it will be applied in, and any additional considerations such as budget. If a given piece, for instance, is to be made using a material with a high chromium content, this makes stainless steel a prime candidate due to its maritime rust-resisting application in saltwater conditions .
Design and Engineering
The first step for any metal manufacturing project is a long and detailed design and engineering process in which every detail matters. Working in Computer Aided Design software, engineers and designers cover every part of the sheet and assembly by considering thermal expansion, load conditions, and assembly application in order to create the strongest, most feasible design. One example may be offered in the provision of custom computer server enclosures. Here, the part must cover the entirety of electronic parts yet also have sufficient heat removal constructs while still being easy to maintain and replace for inspection, maintenance, or replacement. Here, the engineers would simulate conditions in question to get the optimal design prior to any metal cutting being performed.
Cutting and Laser Cutting
The next step is cutting, and here, the selected metal sheets are taken to their original forms. Now, cutting is done using laser light, a technique that many modern facilities employ. Laser cutting is fast, and it is highly accurate. For example, the laser cutting machine can accurately cut thin and thick sheets of metal up to 25mm at a time. The machines can cut metal with an accuracy level of several millimeters. More importantly, laser cutting technology can create complex cuts that the other methods cannot sustain. They can cut delicate patterns on a metal facade, for example, or create logos of a company for corporate signage on the building. This means that very little waste is left, and there is high efficiency at this stage.
Forming and Bending
Forming is another important phase in this process, for this is where the real shape is taken. There are different ways to form the metal, one of them air bending and another one, coin bending. Step 1 is to position the sheet metal to be formed to the press brake. The next step follows, in which just the right amount of force is used to the metal to make it conform to the shape of the tool. When creating a seamless bend on an architectural metal panel, for example, the angle and the finish must be perfect, a process that requires careful planning and professional completion. These process, like step 2 bending depends heavily on the level of technology and the experience and solidity of the operator. In other cases, the process may involve bending by use of the hammer or any other method in manual bending.
Finishing and Quality Control
Finishing is the last part of the fabrication process, including powder coating, or anodizing, which improves the appearance and prevents the product from environmental hazards. Quality control is severe, implying particular examination of every detail. It might be checking in tactile measuring systems to ensure dimensional integrity or visual control to make sure the surface finish matches the client’s needs. Each part should undergo the scrutiny before being carried out to the customer, turning out to be defect-free. Each stage of precision sheet metal fabrication is connected, and performing it requires significant knowledge and skill to create usable items that also look good.
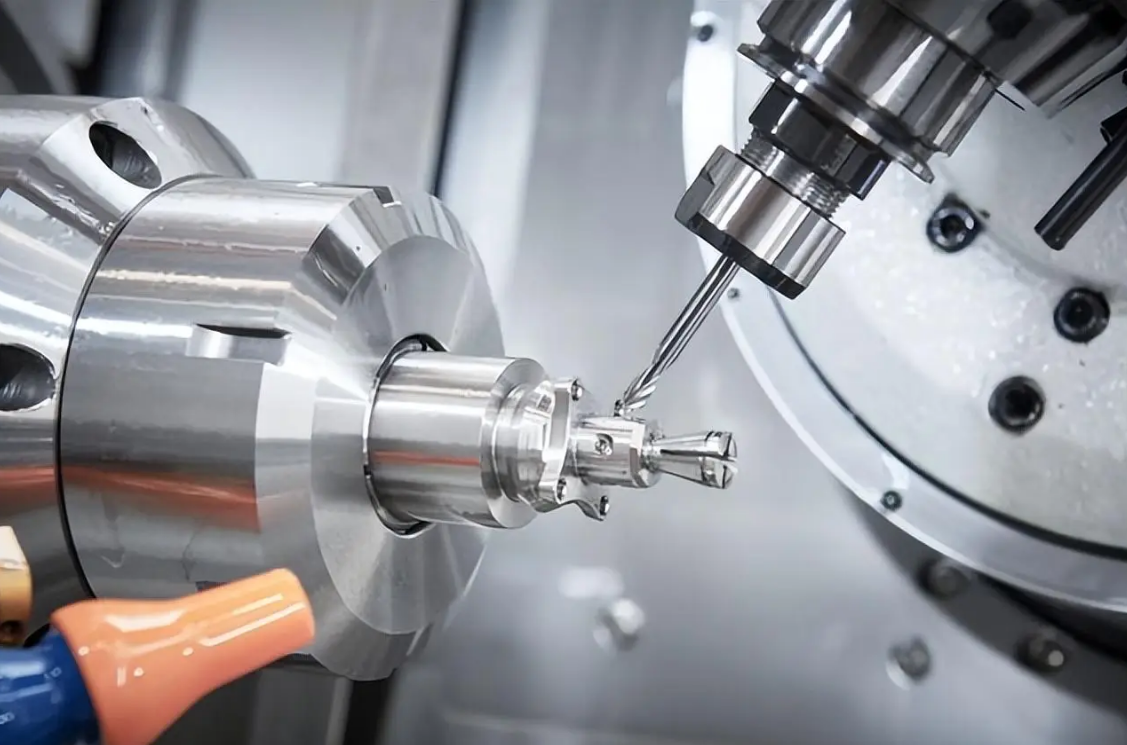
Cutting and Laser Cutting
The cutting stage is where precision really starts to come into play in sheet metal fabrication. Typically, this involves the use of high-tech equipment to ensure each cut is exactly right and meets the strict specifications the project needs. Laser cutting is by far the most precise technique and also excels in handling extremely fine work efficiently.
Traditional Cutting Techniques
Before the advent of laser technology, the main ways of cutting included shearing or sawing, and are still widely used today for simpler tasks and cases when the materials cannot be cut by laser PVC, for example. Shearing involves running a cutting blade over a large sheet of metal and can only be used for straight-line cuts. It is a relatively simple and thus cost-effective way to cut metal to size.
Laser Cutting Technology
The main feature of the technology is the use of a high-power laser to cut metal with extreme precision. Under the process:
-
First, the machine is programmed with CAD models representing the shape to be cut. The primary quality to remember is that the edge that is cut is determined by the material, not the machine, which is why several options could be applied if a piece contains sheets of more than one material.
-
Next, settings are selected for the laser, based on whether the material to be cut is of one or another type and how thick it is: lasers are typically capable of cutting metal sheets between 0.5mm and 25mm.
-
The actual cut then involves the laser precisely following the programmed path. This delivery mode allows a tolerance of ±0.1mm thanks to the machines’ precision .
The technology is efficient in accomplishing clean, fine cuts, making the need for any finishing less frequent. It is exceptional in fabricating fine and extremely dense detail, such as architectural metal decorations with very intricate patterns or specific, tiny metal parts for electronics. The degree of precision does not only improve the quality but also the efficiency of the fabrication: being an automated procedure, it is also impressively fast and boosts the production cycle, which is commonly crucial for projects involving sheet metal.
Forming and Bending
Forming and bending operations are critical to precision sheet metal fabrication as they make a flat piece of sheet metal conform to tight specifications by turning it into a variety of complex shapes. The process is possible because of quality machinery and advanced equipment that can manipulate the metal without removing any material, which guarantees the product preserved integrity and exact dimensions. Different ways used in processing include air bending, coin bending, roll forming and others. Each has its specifics depending on the final shape required with air bending allowing to produce V-shape, U-shape, and channel shape profiles. In coin bending, the sheet metal is squeezed between a punch and a die line and a coin, which is perfect for a tight bend with high precision. In roll forming, the sheet metal is forced through a series of rolls to produce elongated equijoin shapes . Some main steps in the process are preparation, table or machine set-up, locating sheet metal into the machine, and the act of bending .
The overall sequence may differ depending on the characteristics of the work, but, in general, each system generally follows a similar set of activities. Rolling, pressing or stamping the material into the required shapes defines forming and bending mechanism . For example, in manufacturing a precision bracket to be used in airplanes and helicopters, each individual bend must be accurate so that it fits accurately and seamlessly in the creation of the larger product . Frequently those tolerances will be with a few ten-thousandths of a millimeter.
Material Considerations and Challenges
Different metals have different qualities regards their reactions to stress. For example, aluminum is more malleable and can be bent easily when compared to stainless steel which needs quite some force to bend. However, stainless steel is more preferred and is used most because with the excess force aluminum will crack and break. An engineer must have in mind the thickness of the material to be bent, the radius of the bend and the type of bend required. The consideration of this factor provides that the right method and machinery are used to bend the material.
Quality control
Quality of the product formed should be maintained and this starts at the forming and bending stage. An inspection of each component produced is carried out to verify that its dimensions and angles are as per the customer’s design. Normally visual inspection is carried out in addition to the use of digital measuring device. Additionally, the operator plays a significant role in the forming and bending stages. In forming, he/she must correctly adjust the machine to produce the required shape while the bending stage requires the operator to handle the material properly such that it is not scratched or dented.
In summary, as examined above, forming and bending in precision sheet metal fabrication are quite challenging but are the process through which the best finishing is achieved. While some of the procedures require technical know-how, all require high level of accuracy to form and bend metals that meet the indicated customer specification.
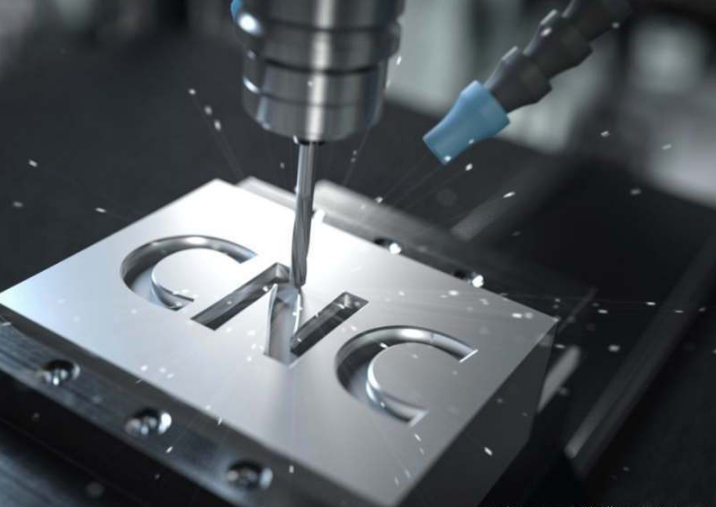
Welding and Assembly
Welding and assembly are the stages where precise sheet metal components form a coherent final product. They require a combination of masterful craftsmanship and technology to ensure that each joint is secure and each assembly meets the demanding standards of quality applicable to the automotive, aerospace, or construction industries.
Welding Techniques and Applications
Welding is a basic fabrication technique underpinning the creation of any metal structure where strong, enduring joints are a necessity. The main types of welding are TIG or tungsten inert gas welding, MIG or metal inert gas welding, and spot welding. TIG welding is generally cleaner and more precise, which makes it perfect for joining stainless steel or aluminum . MIG welding is more rapid and has a stronger bond, which makes it superb for thicker metal assemblies, such as in construction equipment. Spot welding is used to ensure that parts are held firmly together using a number of small welds of high electrical resistance.
Assembly Line Setup
The process generally follows a simple sequence of operations designed to achieve maximum efficiency:
Arrangement of all components to be assembled, ensuring that each part is within reach.
Tacking of all parts to keep them locked in place.
Systematic welding of all joints.
Inspection of each weld to check their integrity. In the case of an automotive frame, a failure to weld properly is unacceptable because the frame must meet a number of very precise specifications bringing the suspension, the drivetrain, and the driver together in a smooth, seamless whole.
Challenges in Welding and Assembly
Perhaps the most significant challenge is the thermal distortion welding inevitably brings. Heating and rapid cooling can irreparably alter the properties of the metals or, at the very least, warp the entire structure. Controlling that distortion usually involves a careful planning of heating and cooling and the use of customized fixtures, such as stopoff plates and spacer tools. Another problem is the very high level of quality assurance involved:
Visual inspection of all surface details
Ultrasonic testing for internal flaws
X-ray testing to verify the impeccable quality of critical bonds.
In the case of a pressure vessel for a nuclear power plant, the tests are so precise that there can be no margin of error – any weld that looks unflawed but is, in truth, slightly porous will result in the deaths of hundreds or thousands of people. These standards mean that assembly technicians and welders must be rigorously trained and recertified at regular intervals to ensure that that high level of skill is never eroded. Overall, welding and assembly does not merely mean putting parts together – it means creating something larger and functionally different than its components. It is a process that, more than any other part of sheet metal fabrication, requires a profound understanding of the materials and their use.